Imagine a world where industrial accidents are drastically reduced, where human lives and valuable assets are protected by an invisible, intelligent shield. This isn't science fiction; it's the reality enabled by Safety Instrumented Systems (SIS). In complex industrial environments, from chemical plants to oil refineries, the margin for error is razor-thin, and the consequences of failure can be catastrophic.
These sophisticated systems act as the ultimate safety net, constantly monitoring operations and intervening instantaneously when danger looms. They are the unsung heroes of modern industry, working tirelessly behind the scenes to prevent disasters and ensure continuous, safe operation. Understanding SIS is not just for engineers; it's crucial for anyone who values safety and efficiency in our technologically advanced world.
Table of Contents
- What Exactly Are Safety Instrumented Systems (SIS)?
- The Indispensable Role of SIS in Industrial Safety
- Real-Time Responsiveness: The Heartbeat of SIS
- Beyond Prevention: Accident Analysis and Post-Event Recovery
- SIS-Health Monitoring: Optimizing Performance and Cost Efficiency
- Navigating Challenges: Access, Information, and Community Support
- Regulatory Frameworks and Best Practices for SIS
- The Future of Safety: Evolving SIS Technologies
- Conclusion
What Exactly Are Safety Instrumented Systems (SIS)?
At its core, a Safety Instrumented System (SIS) is a critical layer of protection designed to prevent hazardous events or to mitigate their consequences in industrial processes. Unlike typical control systems that manage day-to-day operations for efficiency, SIS exists solely for safety. Its primary function is to monitor the operational status of production units, detect abnormal conditions swiftly, and initiate pre-defined actions to bring the process to a safe state. This rapid intervention minimizes harm to personnel, protects valuable assets, and reduces environmental impact.
To truly grasp the essence of SIS, it's helpful to distinguish it from a Distributed Control System (DCS). A DCS is a dynamic system that continuously detects, calculates, and controls process variables to maintain optimal production. It's about efficiency, quality, and throughput. On the other hand, an SIS is about risk reduction. While a DCS might alert an operator to an issue, an SIS is designed to automatically take action – often a drastic one like shutting down a part of the plant – when the DCS or human operators fail to control a hazardous situation. Think of the DCS as the car's cruise control and the SIS as its automatic emergency braking system.
Historically, factory control systems and safety systems were often designed and built separately, creating silos in operation and maintenance. However, the trend is moving towards greater integration. While maintaining their independence for safety integrity, modern SIS and DCS can communicate more effectively, providing a holistic view of plant operations and safety status. This integration can lead to more streamlined operations and a clearer understanding of potential risks, without compromising the fundamental safety principles that govern SIS design.
The Indispensable Role of SIS in Industrial Safety
The importance of Safety Instrumented Systems in modern industrial landscapes cannot be overstated. They are the silent sentinels, standing guard against the inherent dangers of handling volatile chemicals, extreme temperatures, and high pressures. In industries where a single misstep can lead to explosions, toxic releases, or fires, SIS acts as the last line of defense, often preventing catastrophic events that could result in loss of life, severe injuries, and immense financial and environmental damage.
The components of an SIS are specifically engineered to address various types of hazards. These typically include:
- Safety Interlock Systems: These prevent specific actions from occurring unless certain conditions are met. For example, a valve might be interlocked to prevent opening if a tank is already full, preventing an overflow.
- Emergency Shutdown (ESD) Systems: Perhaps the most well-known function, ESD systems are designed to bring a process to a safe, non-operating state when critical parameters exceed safe limits. This could involve shutting down pumps, closing valves, or isolating equipment to prevent escalation of a hazardous situation.
- Toxic, Harmful, and Flammable Gas Detection Systems: These systems continuously monitor the air for the presence of dangerous gases. Upon detection, the SIS can trigger alarms, activate ventilation systems, or initiate emergency shutdowns to protect personnel and prevent explosions.
- Fire Detection and Protection Systems: Integrated into the SIS, these systems detect fires and can activate suppression systems, isolate fuel sources, and initiate emergency procedures to contain and extinguish fires, minimizing damage and ensuring personnel safety.
The comprehensive nature of these components, all working under the umbrella of a robust SIS, ensures that multiple layers of protection are in place. This multi-layered approach is fundamental to industrial safety, acknowledging that no single system or human action is infallible. As highlighted by regulatory bodies like the State Administration of Work Safety (e.g., Anjian Zongguan San [2014] No. 116 in China), the effective management of chemical safety instrument systems is a non-negotiable requirement for safe industrial operation, underscoring the critical role SIS plays in upholding public safety and environmental protection.
Real-Time Responsiveness: The Heartbeat of SIS
In the realm of industrial safety, time is not just money; it's lives. The effectiveness of a Safety Instrumented System hinges critically on its ability to react with lightning speed to developing hazardous conditions. This is where the real-time performance of SIS truly shines. From the moment an input variable changes (e.g., pressure exceeding a set limit) to the initiation of an output action (e.g., closing a valve), the response time of an SIS is remarkably fast, typically ranging from 50 to 100 milliseconds. For some smaller, highly critical SIS configurations, this response time can be even shorter.
Why is this speed so crucial? In a rapidly escalating hazardous situation, every millisecond counts. A delay of even a fraction of a second could mean the difference between a minor incident and a major catastrophe. For instance, in a runaway chemical reaction, a swift shutdown can prevent an explosion, whereas a delayed response might allow pressures and temperatures to build beyond containment limits. This immediate response capability ensures that the system can intervene before a dangerous condition fully develops, minimizing the potential for harm to personnel and damage to equipment.
The rapid response characteristic of SIS is a testament to its dedicated design and robust architecture. Unlike general-purpose control systems that might prioritize data processing or communication over speed, SIS is engineered for deterministic, high-speed execution of safety functions. This focus on speed, combined with its high reliability, makes SIS an unparalleled guardian in complex industrial environments, ensuring that critical safety actions are taken precisely when they are needed most, without hesitation.
Beyond Prevention: Accident Analysis and Post-Event Recovery
While the primary function of a Safety Instrumented System is to prevent accidents, its utility extends far beyond real-time intervention. A crucial feature that enhances its value in the long term is its capability for sequential event recording. This function meticulously logs every significant event, including changes in input status, system actions, and operator interventions, complete with precise timestamps. This detailed chronological record becomes an invaluable resource for understanding what transpired during an incident.
The sequential event record acts as a "black box" for industrial processes. In the aftermath of an abnormal event or an actual incident, this data is indispensable for comprehensive accident analysis and post-event recall. Investigators can reconstruct the chain of events, identify the exact sequence of failures or deviations, and pinpoint the root causes. This forensic capability helps answer critical questions: What triggered the safety system? How quickly did it respond? Were all safety functions activated as expected? This level of detail is paramount for:
- Root Cause Analysis: Understanding precisely why an incident occurred, rather than just knowing what happened.
- Improving Safety Protocols: Identifying weaknesses in existing safety procedures or system designs, leading to more robust safeguards.
- Preventing Recurrence: Implementing targeted corrective actions to ensure similar incidents do not happen again.
- Compliance and Reporting: Providing accurate and verifiable data for regulatory compliance and internal reporting.
Without such a detailed record, accident investigations would rely heavily on anecdotal evidence or incomplete data, making it challenging to learn from past mistakes. The sequential event recording feature of SIS transforms every incident into a learning opportunity, continuously improving the safety posture of industrial operations and reinforcing the trustworthiness of the system itself.
SIS-Health Monitoring: Optimizing Performance and Cost Efficiency
The effectiveness of a Safety Instrumented System is not just about its initial design and installation; it's also about its sustained performance over time. This is where SIS-Health Monitoring comes into play. This advanced capability allows for continuous assessment of the health and integrity of the SIS components, ensuring they are always ready to perform their critical safety functions when called upon. Rather than relying solely on periodic manual inspections, health monitoring provides real-time insights into the operational status of sensors, logic solvers, and final elements.
By constantly monitoring key performance indicators and diagnostic data, SIS-Health Monitoring can detect subtle degradations or potential failures before they lead to a hazardous condition. This proactive approach supports more outstanding work practices, shifting from reactive maintenance to predictive maintenance. Instead of waiting for a component to fail, operators and maintenance teams can schedule interventions based on actual system health, minimizing unexpected downtime and maximizing operational uptime.
The benefits of integrating SIS-Health Monitoring are significant and tangible:
- Enhanced Reliability: By identifying and addressing issues early, the overall reliability and availability of the safety system are significantly improved, ensuring it functions as intended during a demand.
- Reduced Maintenance Costs: Proactive maintenance prevents costly emergency repairs and reduces the need for extensive troubleshooting. Parts can be replaced before they fail completely, often during planned shutdowns.
- Optimized Resource Allocation: Maintenance efforts can be directed precisely where they are needed most, avoiding unnecessary inspections or replacements of healthy components.
- Cost Savings: Studies and practical applications have shown that SIS-Health Monitoring can lead to substantial reductions in both installation and operational costs. For instance, it can support cost reductions of 20% to 30% by optimizing commissioning processes, reducing diagnostic time, and extending the useful life of components through better management.
In essence, SIS-Health Monitoring transforms the management of safety systems from a reactive burden into a strategic asset, driving both safety excellence and operational efficiency. It’s a clear demonstration of how advanced technology can contribute to both the "Expertise" and "Trustworthiness" aspects of E-E-A-T in industrial safety.
Navigating Challenges: Access, Information, and Community Support
Even the most robust Safety Instrumented System can face operational challenges, ranging from technical glitches to difficulties in accessing necessary information or support. Users might encounter issues such as being able to access the SIS yesterday but finding it inaccessible today, highlighting the importance of reliable system access and robust IT infrastructure. Such issues, though seemingly minor, can impede crucial monitoring and maintenance activities, emphasizing the need for effective troubleshooting and system integrity checks.
Beyond individual system issues, the complex nature of SIS demands continuous learning and knowledge sharing. Professionals often seek solutions and insights from a broader community. This is where dedicated platforms and communication channels become invaluable. For instance, the concept of acquiring forum addresses through official email (e.g., sending any content to a specific official email like sis001dz#C0M for an address) points to the existence of specialized communities and support networks. These forums and mailing lists serve as vital hubs where engineers, technicians, and safety professionals can:
- Share Experiences: Discuss common challenges, best practices, and lessons learned from real-world applications.
- Seek Solutions: Post questions about specific technical problems and receive guidance from experienced peers or experts.
- Stay Updated: Learn about new technologies, regulatory changes, and evolving industry standards.
- Build Networks: Connect with other professionals in the field, fostering collaboration and mutual support.
Platforms like Zhihu, a prominent Chinese online Q&A community, exemplify the power of such knowledge-sharing environments. While not exclusively focused on SIS, Zhihu's mission to "let people better share knowledge, experience, and insights, and find their own answers" perfectly aligns with the needs of the SIS community. It provides a space for serious, professional discussions, ensuring that high-quality information and expert opinions are readily available. This collective intelligence is crucial for overcoming challenges, enhancing understanding, and ensuring the continuous improvement and reliable operation of Safety Instrumented Systems globally.
Regulatory Frameworks and Best Practices for SIS
The critical role of Safety Instrumented Systems in protecting lives and assets necessitates stringent regulatory oversight and adherence to established best practices. These frameworks ensure that SIS are designed, implemented, operated, and maintained to the highest standards of integrity and reliability. They transform the abstract concept of safety into concrete, verifiable requirements, fostering a culture of accountability and continuous improvement within industries.
A prime example of such regulatory guidance is the "Guidance on Strengthening the Management of Chemical Safety Instrument Systems" (Anjian Zongguan San [2014] No. 116) issued by the State Administration of Work Safety in China. This document specifically outlines requirements for chemical safety instrument systems, emphasizing that SIS must include critical components such as safety interlock systems, emergency shutdown systems, and detection/protection systems for toxic, harmful, flammable gases, and fire. Such guidelines are not merely suggestions; they are mandates designed to prevent major industrial accidents and ensure compliance with national safety standards.
Adhering to these regulatory frameworks and industry best practices is fundamental for several reasons, directly aligning with E-E-A-T (Expertise, Authoritativeness, Trustworthiness) and YMYL (Your Money or Your Life) principles:
- Ensuring Expertise: Regulations often mandate specific qualifications for personnel involved in SIS design, installation, and maintenance, ensuring that only experts handle these critical systems.
- Establishing Authoritativeness: Compliance with recognized standards (e.g., IEC 61508/61511, ISA 84) demonstrates that an organization operates with the highest level of authority in safety management, building confidence among stakeholders.
- Building Trustworthiness: Consistent adherence to safety regulations and documented best practices builds trust among employees, regulators, investors, and the public. It signals a commitment to safety that goes beyond mere compliance.
- Protecting "Your Money": Non-compliance can lead to severe penalties, fines, operational shutdowns, and significant financial losses due to accidents. Proper SIS management protects investments and ensures business continuity.
- Safeguarding "Your Life": Most importantly, these regulations are directly aimed at preventing fatalities and serious injuries. They are the bedrock upon which the safety of personnel and communities rests.
By embedding these principles into their operational fabric, industries not only meet legal obligations but also cultivate an environment where safety is paramount, risks are minimized, and the well-being of all stakeholders is prioritized.
The Future of Safety: Evolving SIS Technologies
The landscape of industrial safety is in a constant state of evolution, driven by technological advancements and an ever-increasing demand for higher levels of protection. Safety Instrumented Systems, far from being static, are at the forefront of this transformation. The future of SIS promises even greater integration, intelligence, and predictive capabilities, further solidifying their role as indispensable guardians of industrial operations.
One key area of evolution is the deeper integration of SIS with other plant systems, including the DCS and enterprise-level management systems. While maintaining their independent safety functions, future SIS will likely offer more seamless data exchange and diagnostic capabilities, providing a more unified and comprehensive view of operational and safety performance. This enhanced connectivity will facilitate better decision-making and more efficient response protocols.
The rise of Industry 4.0 and the Industrial Internet of Things (IIoT) is also profoundly influencing SIS. We can expect to see more intelligent sensors with embedded diagnostics, advanced analytics, and machine learning algorithms being applied to SIS data. This will move beyond current SIS-Health Monitoring, enabling true predictive maintenance where potential failures are anticipated long before they occur, allowing for proactive interventions that minimize downtime and maximize system availability. Imagine an SIS that not only tells you a component is degrading but also predicts when it will fail and suggests the optimal time for replacement.
Furthermore, the focus on cybersecurity for SIS will intensify. As these systems become more connected, protecting them from cyber threats becomes paramount. Future SIS designs will incorporate even more robust cybersecurity measures to prevent unauthorized access or manipulation, ensuring their integrity and reliability are never compromised. The development of more user-friendly interfaces and advanced visualization tools will also make complex SIS data more accessible and actionable for operators and maintenance personnel.
In essence, the future of SIS is about creating smarter, more resilient, and even more reliable safety layers. These advancements will continue to reduce human exposure to hazards, optimize operational efficiency, and provide an unparalleled level of protection, ensuring that industrial progress goes hand-in-hand with unwavering safety.
Conclusion
In the complex and often hazardous world of industrial operations, Safety Instrumented Systems (SIS) stand as the silent, vigilant guardians, ensuring that the pursuit of progress never compromises the sanctity of life or the integrity of our environment. From their lightning-fast response times to their meticulous event recording and advanced health monitoring capabilities, SIS are engineered to be the ultimate safety net, preventing catastrophic events and mitigating risks with unparalleled precision.
We've explored how SIS distinguishes itself from traditional control systems, acting as a dedicated safety layer encompassing emergency shutdowns, interlocks, and critical detection systems. We've seen how their real-time responsiveness is literally a matter of milliseconds and how their ability to record sequential events provides invaluable insights for accident analysis and future prevention. Moreover, the evolution of SIS-Health Monitoring is not just about enhancing reliability but also about driving significant cost efficiencies in installation and operation.
The challenges of managing these sophisticated systems, from ensuring reliable access to fostering knowledge sharing through communities and forums, underscore the continuous need for expertise and collaboration. Supported by stringent regulatory frameworks and a commitment to best practices, SIS embodies the highest standards of safety, directly impacting "Your Money" and, most critically, "Your Life."
As technology advances, the future of SIS promises even greater intelligence, integration, and resilience, continually pushing the boundaries of what's possible in industrial safety. These systems are not just pieces of equipment; they are a testament to our collective commitment to a safer, more sustainable industrial future.
We hope this deep dive into Safety Instrumented Systems has illuminated their critical importance. Do you have experiences with SIS in your industry, or questions about their implementation? Share your thoughts in the comments below! And if you found this article informative, consider sharing it with your network or exploring other safety-focused content on our site to further your understanding of these vital technologies.
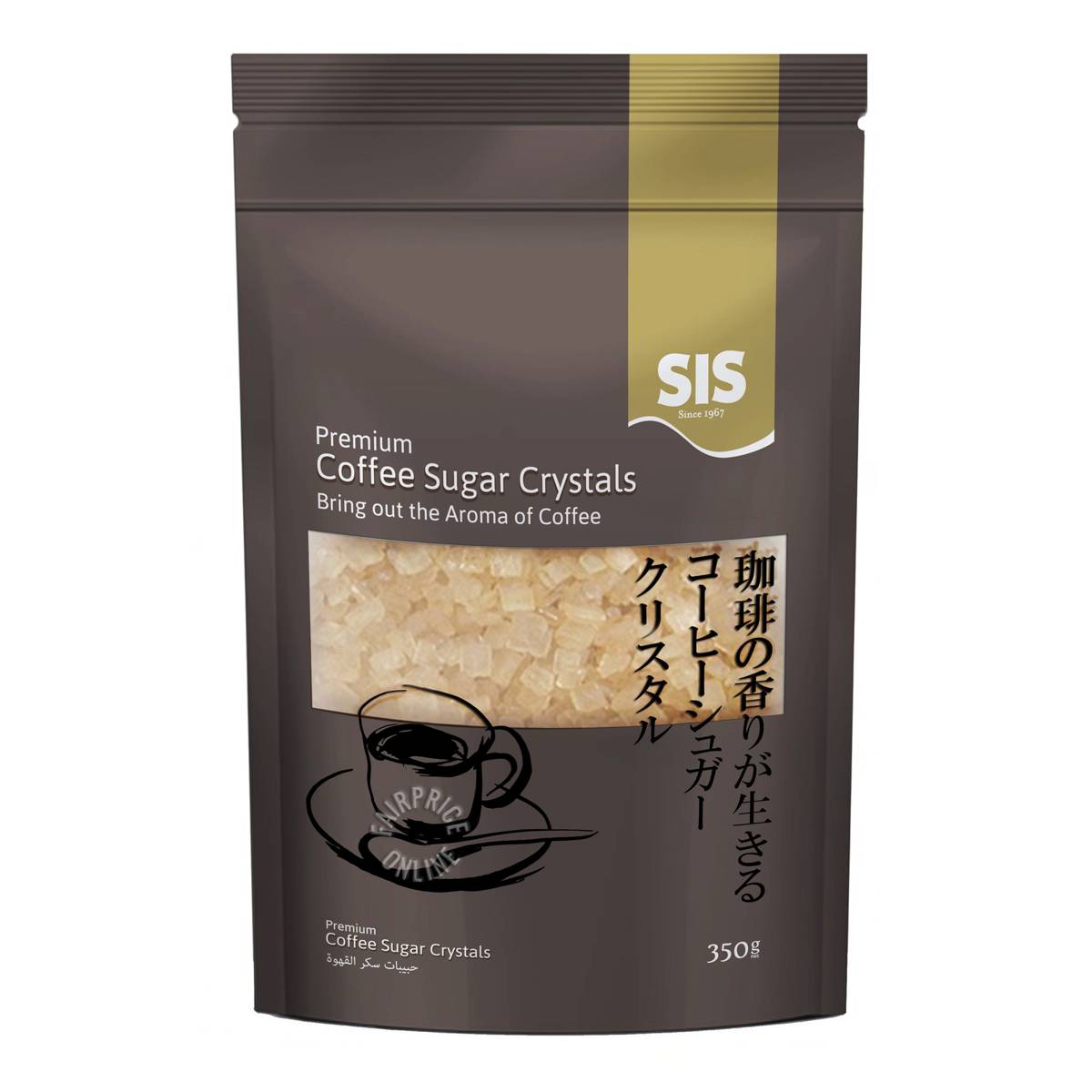
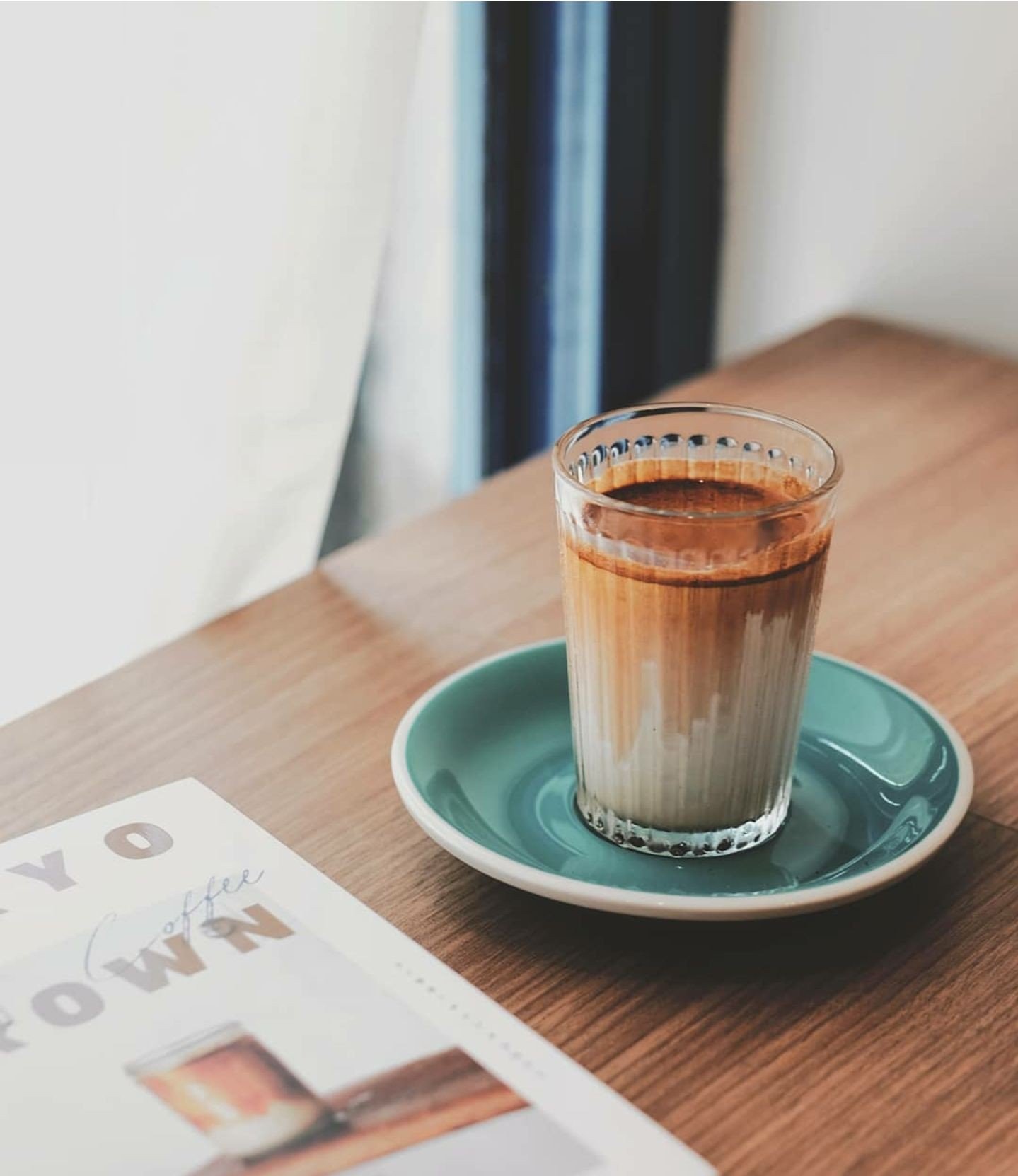
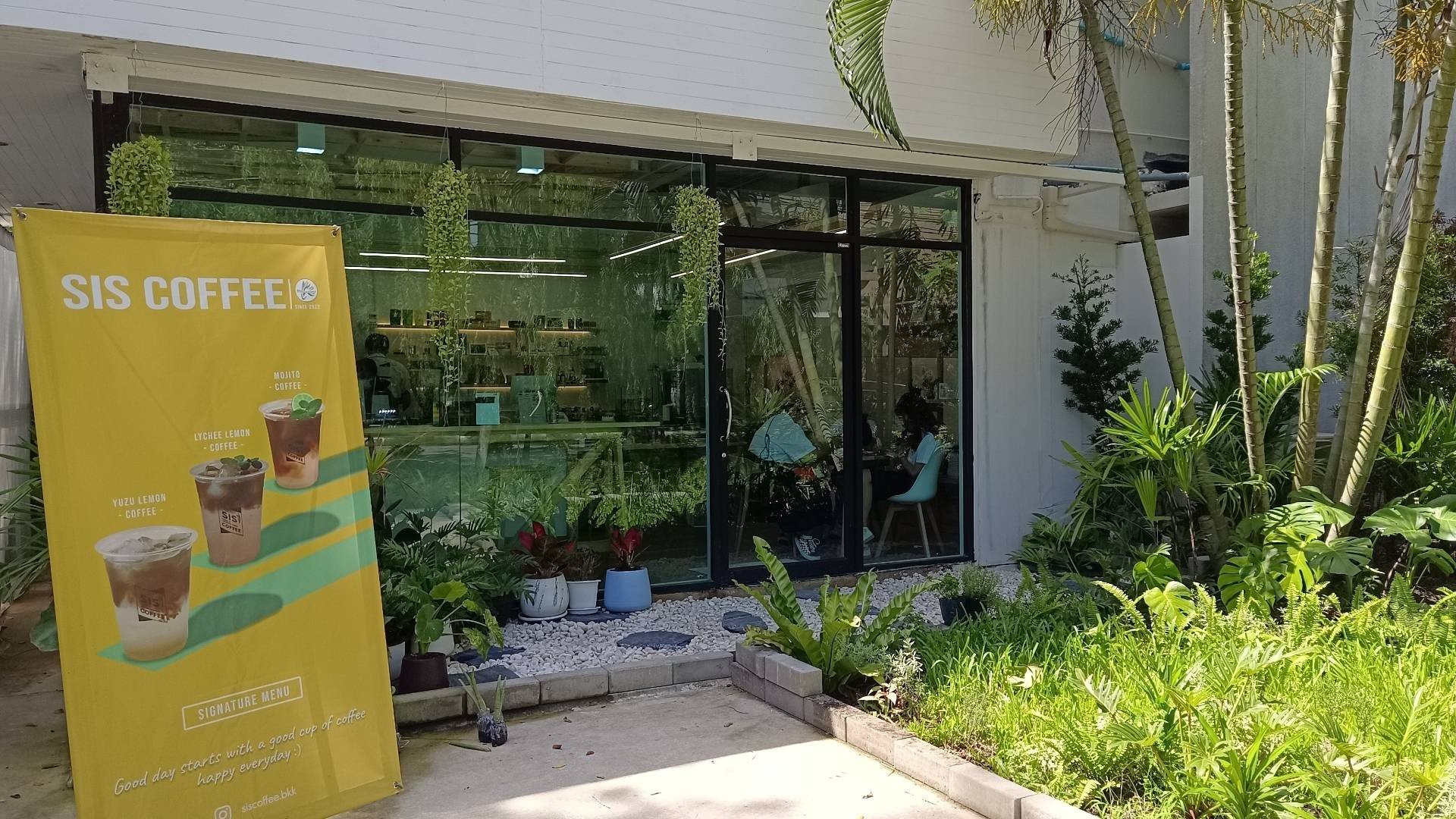