**In the intricate world of manufacturing and industrial processes, where materials are meticulously handled and transformed, a fascinating yet often overlooked component plays a pivotal role in ensuring smooth operations and impeccable product quality. This unsung hero, known colloquially as the "winding dancer," embodies a remarkable blend of mechanical ingenuity and dynamic responsiveness. Far from a literal performer, the winding dancer is a critical engineering element, a testament to how subtle movements can dictate the success of large-scale production, ensuring that materials like wire, film, fabric, or paper are spooled and processed with unwavering precision.** This article delves deep into the essence of the winding dancer, exploring its fundamental principles, diverse applications, and indispensable contribution to modern industry. We will unravel the concept of "winding" itself, drawing from its various definitions – from the coiling of a material around an object to the intricate path of an electrical current. By understanding the core mechanics of winding and the dynamic role of the dancer, we can truly appreciate the silent, rhythmic ballet it performs within countless industrial machines, safeguarding efficiency, preventing costly errors, and ultimately enhancing the quality of products we rely on daily. ---
Table of Contents
- What is Winding? Deciphering the Core Concept
- The Winding Dancer: An Engineering Marvel
- Anatomy of a Winding Dancer System
- Diverse Applications: Where the Dancer Performs
- The Engineering Principles Behind the Dance
- Economic and Quality Impact of the Winding Dancer
- Maintaining the Rhythm: Care and Troubleshooting
- The Future of Winding Systems and the Dancer
What is Winding? Deciphering the Core Concept
Before we delve into the specifics of the "winding dancer," it's crucial to establish a clear understanding of "winding" itself. The term "winding" is remarkably versatile, encompassing a range of actions and states, all revolving around the concept of turning or coiling. At its most fundamental, winding refers to the act of wrapping or turning something, often in a spiral, around an object or axis. Think of it as the meticulous process of creating order from a continuous length of material. In a mechanical context, winding often describes material, such as wire or thread, wound or coiled about an object, like an armature. This can be a single turn of the wound material, or a continuous coil through which an electric current can pass, as famously used in transformers and generators. These electrical applications rely on precisely laid windings to create a symmetrically laid, electrically conducting current path. Beyond the technical, "winding" can also describe a path, road, or river that repeatedly turns in different directions, characterized by its twists and turns. This imagery of a winding country road or a winding mountain stream helps us visualize the dynamic, non-linear movement that is inherent in the concept. Essentially, a winding is something which is coiled, twisted, or plaited, or a length of substance wound around something else, with the way in which something is wound being as important as the act itself. This multifaceted definition lays the groundwork for understanding the complex role of the winding dancer.The Winding Dancer: An Engineering Marvel
The "winding dancer," also commonly known as a dancer arm or dancer roller, is a critical component in machinery designed to handle continuous web materials, such as film, paper, textiles, wire, and cable. Its name perfectly encapsulates its function: it "dances" or moves dynamically in response to changes in material tension or speed, maintaining a consistent, controlled environment for the winding or unwinding process. This seemingly simple mechanism is, in fact, a sophisticated feedback loop that prevents material breakage, ensures uniform product quality, and optimizes machine throughput. Without the winding dancer, many high-speed industrial processes would be impossible, leading to frequent material jams, inconsistent product dimensions, and significant waste. It’s a testament to engineering elegance, providing stability in a system inherently prone to dynamic fluctuations.Dynamic Tension Control: The Dancer's Primary Role
The primary function of a winding dancer is dynamic tension control. In any continuous winding or unwinding operation, maintaining a consistent material tension is paramount. Too much tension can stretch, deform, or even break the material, leading to costly downtime and scrap. Too little tension can result in slack, wrinkling, or uneven winding, compromising product quality. The winding dancer acts as a real-time buffer, absorbing momentary variations in material speed or tension. As the material passes over the dancer roller, the arm or roller moves up or down. This movement is then translated into a signal (often electrical or pneumatic) that adjusts the speed of the motor driving the unwind or rewind roll, or controls a brake, ensuring that the tension remains within a precise, predetermined range. This constant, subtle adjustment is what makes the "dancer" so vital – it's continuously adapting, much like a skilled dancer adjusting their balance.Accumulation and Buffering: Smoothing the Flow
Beyond tension control, the winding dancer also serves a crucial role in accumulation and buffering. In many manufacturing lines, different stages of the process operate at varying speeds or require momentary stops. For instance, a printing press might momentarily slow down for a plate change, while the upstream unwinder continues to feed material. Without a buffer, the material would either snap or pile up uncontrollably. The winding dancer system, with its ability to move through a range of motion, effectively creates a temporary storage loop for the material. When the downstream process slows, the dancer arm rises, accumulating excess material. When the downstream process speeds up, the dancer arm falls, releasing the stored material. This buffering capability ensures a continuous, smooth flow of material through the entire production line, minimizing disruptions and maximizing efficiency. It's like a shock absorber for the material flow, preventing jarring stops and starts.Anatomy of a Winding Dancer System
A typical winding dancer system comprises several key components working in concert. At its heart is the **dancer roller or arm**, which is a lightweight, low-friction roller mounted on a pivot or linear slide. The material being processed wraps around this roller. The position of this dancer arm is crucial; it's often connected to a **sensor** – which could be a potentiometer, an encoder, or a proximity sensor – that continuously monitors its precise location. This sensor sends feedback to a **controller** (e.g., a PLC or dedicated tension controller). The controller then processes this information and sends commands to an **actuator**, which is typically a motor (for driven rolls) or a brake (for unwinding rolls). For instance, if the dancer arm drops below its setpoint, indicating a loss of tension or an increase in material demand, the sensor signals the controller. The controller then commands the unwind motor to speed up, or the rewind motor to slow down, or the brake to reduce its force, thereby restoring the desired tension and returning the dancer arm to its optimal position. Conversely, if the arm rises too high, indicating excess tension or material, the controller makes the opposite adjustments. Some systems also incorporate **pneumatic cylinders or weights** attached to the dancer arm to provide a constant base tension, with the electronic feedback system handling the fine-tuning. The design and calibration of each component are critical to the overall performance and responsiveness of the winding dancer system, ensuring that it can accurately and reliably manage the dynamic forces at play.Diverse Applications: Where the Dancer Performs
The versatility and effectiveness of the winding dancer make it an indispensable component across a vast array of industries. Its ability to precisely control tension and buffer material flow is critical in any process involving continuous web or strand handling. From the delicate threads of a textile mill to the robust cables powering our cities, the winding dancer is quietly performing its essential ballet, ensuring quality and efficiency.Textile and Fabric Processing
In the textile industry, fabrics are delicate and prone to stretching, tearing, or wrinkling if not handled with extreme care. Winding dancers are widely used in processes like dyeing, printing, coating, and slitting. They ensure that the fabric maintains consistent tension as it moves through various treatment baths or printing stations, preventing distortions that could ruin patterns or compromise the material's integrity. For example, during the unwinding of a large fabric roll onto a printing line, the dancer system ensures that the fabric feeds smoothly, preventing slack that could lead to misprints or excessive tension that could stretch the fabric out of shape. This precision is vital for producing high-quality garments and industrial textiles.Film and Packaging Industries
The production of plastic films, foils, and packaging materials relies heavily on precise tension control. These materials are often thin and highly sensitive to tension variations, which can lead to wrinkles, tears, or inconsistent thickness. Winding dancers are integral to laminating machines, slitting machines, and flexible packaging lines. They ensure that multiple layers of film are joined together smoothly without air bubbles or misalignments, and that finished rolls are wound tightly and uniformly. Imagine the precision required for food packaging where airtight seals are paramount; the winding dancer plays a direct role in maintaining the film integrity necessary for such applications, contributing directly to product safety and shelf life.Wire and Cable Manufacturing
In the wire and cable industry, materials range from fine copper strands to heavy-duty power cables. The winding dancer is crucial for maintaining consistent tension during drawing, insulating, and spooling processes. Without it, wires could break, become deformed, or be wound unevenly onto spools, leading to quality issues and production bottlenecks. For instance, during the insulation process, if the wire tension fluctuates, the insulation thickness could become inconsistent, compromising the cable's electrical properties and safety. The winding dancer ensures that the wire maintains its integrity and is wound onto the final spool with perfect symmetry and tension, ready for its intended application, whether it's in electronics, construction, or power transmission.The Engineering Principles Behind the Dance
The effectiveness of the winding dancer is rooted in fundamental engineering principles, primarily feedback control systems and the physics of tension. At its core, the system operates on a closed-loop feedback mechanism. The dancer arm's position provides real-time data about the material's tension state. This data is then compared to a desired setpoint, and any deviation triggers an immediate corrective action. This continuous monitoring and adjustment is what makes the "winding dancer" so responsive and precise. From a physics perspective, the dancer system manages forces. The material itself possesses inertia and elasticity. As the speed of the winding or unwinding changes, these properties come into play. The dancer arm, often designed with minimal friction and mass, is able to quickly react to these changes in force. The mechanical advantage provided by the arm's pivot point, combined with the controlled application of counter-forces (from pneumatic cylinders, weights, or controlled motor torque), allows the system to absorb and release energy efficiently. This dynamic equilibrium ensures that the tension in the material remains constant, preventing stress concentrations that could lead to material failure. Advanced systems may even incorporate predictive algorithms, using data from previous movements to anticipate and preemptively adjust for upcoming changes, further enhancing the system's stability and performance. The elegance lies in its simplicity yet profound impact on complex industrial operations.Economic and Quality Impact of the Winding Dancer
The winding dancer, while a seemingly small component, wields immense influence over the economic viability and product quality of numerous manufacturing operations. Its direct impact on reducing waste, minimizing downtime, and ensuring consistent output translates into significant financial savings and enhanced market competitiveness for businesses. Firstly, by maintaining optimal material tension, the winding dancer drastically reduces material waste. Without precise control, materials like thin films or delicate fabrics can easily stretch, wrinkle, tear, or become misaligned, rendering them unusable. This scrap material represents not only the cost of the raw input but also the energy and labor expended up to that point. A well-functioning winding dancer minimizes these losses, directly improving the bottom line. Secondly, it contributes to higher machine uptime. Breakages and jams due to tension inconsistencies are major causes of production halts. Each minute of downtime translates into lost production and increased labor costs. The dancer's ability to smoothly buffer and control material flow prevents these disruptions, ensuring continuous operation and maximizing throughput. From a quality perspective, the winding dancer is indispensable. It guarantees product uniformity and consistency. Whether it's the even thickness of a plastic film, the precise pattern registration on a printed fabric, or the symmetrical winding of a wire spool, the dancer ensures that every meter of material meets the required specifications. This consistency is crucial for customer satisfaction, brand reputation, and compliance with industry standards. In sectors where product integrity is paramount, such as medical device manufacturing or food packaging, the winding dancer's role in maintaining material quality can even have YMYL (Your Money or Your Life) implications, ensuring product safety and reliability. Its contribution extends far beyond mere mechanics; it underpins the very foundation of efficient, high-quality manufacturing.Maintaining the Rhythm: Care and Troubleshooting
Like any critical mechanical system, the winding dancer requires regular maintenance and occasional troubleshooting to ensure its optimal performance and longevity. Neglecting these aspects can lead to reduced efficiency, increased downtime, and compromised product quality. Proactive maintenance is key to keeping the "dancer" in perfect rhythm. Routine maintenance typically involves inspecting the dancer roller for wear and tear, ensuring that its bearings are smooth and free of obstruction. Lubrication of pivot points and linear slides, if applicable, is also essential to minimize friction and allow for fluid movement. Calibration of the tension sensor should be checked periodically to ensure accurate feedback to the control system. Dust, debris, or material buildup on the roller or in the sensor area can impair performance and should be regularly cleaned. Troubleshooting common issues often involves diagnosing the root cause of tension fluctuations or erratic dancer movement. If the dancer arm is "bouncing" excessively, it might indicate an issue with the control loop tuning, an imbalance in the dancer arm itself, or a problem with the unwind/rewind motor's speed control. If the dancer is stuck or slow to react, it could point to excessive friction in its mechanical components, a faulty sensor, or a problem with the pneumatic pressure (if applicable). Identifying whether the issue is mechanical, electrical, or control-related is the first step. Consulting the machine's manual and, if necessary, seeking expert advice from the equipment manufacturer or a specialized technician, can help resolve complex problems efficiently. Proper care ensures the winding dancer continues its vital work, silently contributing to seamless production.The Future of Winding Systems and the Dancer
As industries continue to push the boundaries of speed, precision, and automation, the winding dancer is also evolving. While its fundamental principle remains the same, advancements in sensor technology, control algorithms, and material science are shaping its future capabilities. The trend towards Industry 4.0 and smart manufacturing means that winding dancer systems are becoming increasingly integrated into larger, interconnected production ecosystems. Future winding dancer systems will likely feature more sophisticated predictive analytics, utilizing machine learning to anticipate material behavior and adjust tension proactively, rather than reactively. This could lead to even greater precision and efficiency, especially with novel, highly sensitive materials. Miniaturization and the development of more compact, energy-efficient dancer systems will also be crucial for increasingly complex and space-constrained production lines. Furthermore, the integration of advanced diagnostics and remote monitoring capabilities will allow for predictive maintenance, minimizing unexpected downtime and optimizing operational costs. The winding dancer, far from being a static component, will continue to "dance" into the future, adapting to new challenges and maintaining its critical role in the intricate world of continuous material processing, ensuring that the "winding" of tomorrow is smoother, faster, and more precise than ever before. ---Conclusion
The "winding dancer" stands as a remarkable example of engineering ingenuity, a silent workhorse that orchestrates the delicate balance of tension and material flow in countless industrial processes. From its foundational role in ensuring the integrity of electrical windings in transformers to its dynamic ballet in high-speed manufacturing lines, its importance cannot be overstated. We've explored how "winding" itself encompasses a spectrum of meanings, from coiled materials to twisting paths, and how the winding dancer leverages these principles to deliver unparalleled precision. Its critical function in dynamic tension control and material buffering directly impacts product quality, reduces waste, and enhances operational efficiency across diverse sectors like textiles, packaging, and wire manufacturing. The winding dancer is more than just a mechanical component; it is a testament to the meticulous attention to detail required in modern production, a crucial element in upholding the E-E-A-T principles of reliability and trustworthiness in manufacturing. Its continuous evolution, driven by advancements in smart technology, promises an even more precise and efficient future for material handling. We hope this exploration has illuminated the vital role of this unsung hero. What other unsung heroes of industry do you find fascinating? Share your thoughts in the comments below, or explore our other articles on industrial automation and precision engineering to deepen your understanding of the intricate world that shapes our everyday products.
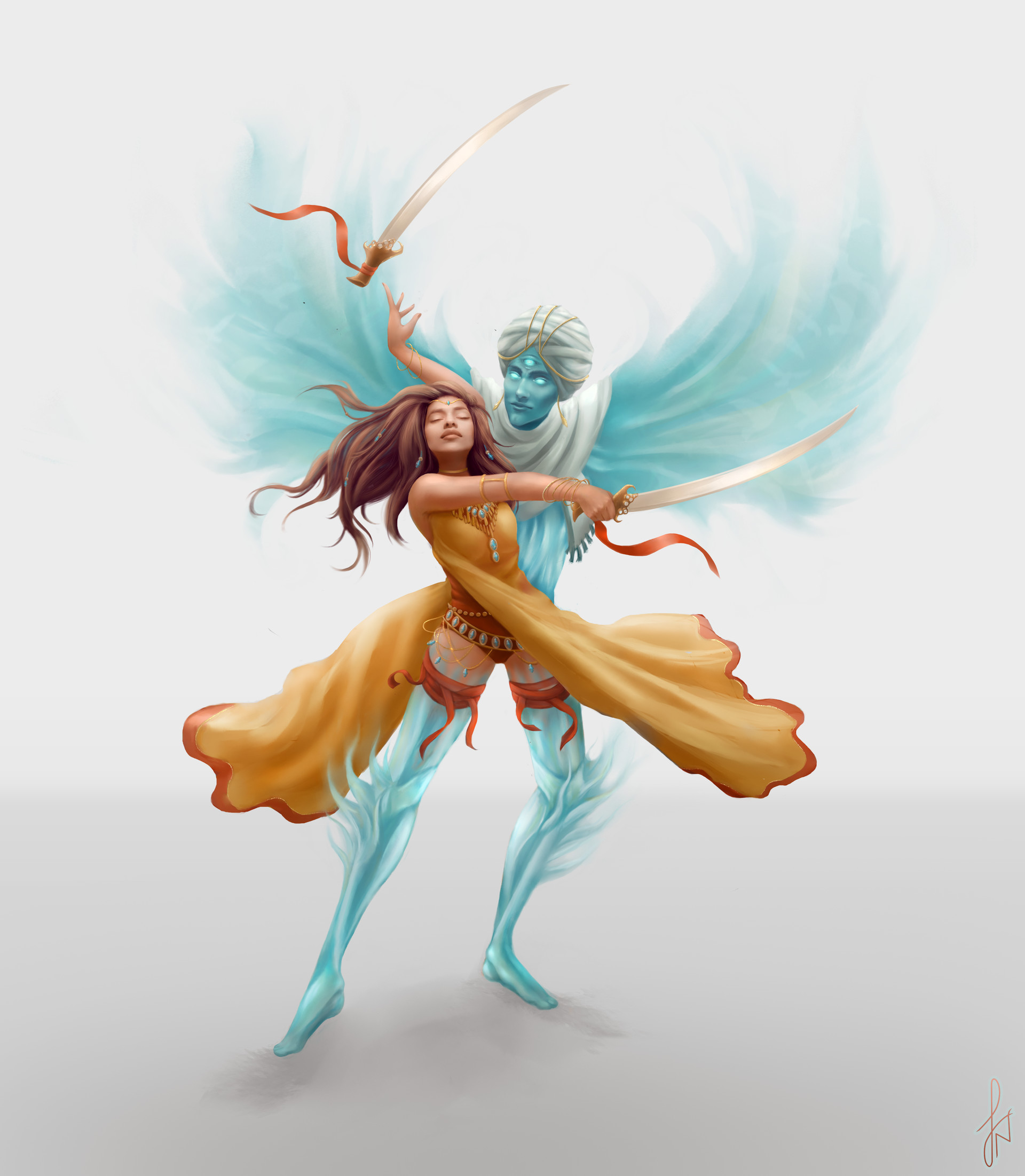