**In the vast landscape of industrial operations, where complex machinery hums and colossal gears turn, one unsung hero stands paramount: the lubricant. More specifically, the industrial-grade lubricant, often found in its most imposing form – the 55 gallon drum of lube. This isn't merely a container of slippery liquid; it's a reservoir of efficiency, a guardian of machinery, and a cornerstone of productivity, ensuring that the wheels of industry turn without a hitch.** This comprehensive guide delves into the world of these essential drums, exploring their significance, the diverse formulations they contain, and how they contribute to the longevity and optimal performance of critical equipment across countless sectors. From reducing friction to protecting against corrosion, the impact of a quality 55-gallon drum of lube resonates throughout the industrial ecosystem, proving itself an indispensable asset.
Table of Contents
- The Unseen Giant: Understanding the 55 Gallon Drum of Lube
- Why a 55-Gallon Drum? Scale, Efficiency, and Economics
- The Diverse World of Industrial Lubricants: Beyond the Basics
- Unpacking the Benefits: Performance, Protection, and Longevity
- Choosing the Right Lube: Navigating Specifications and Certifications
- Sourcing Your Industrial Lube: Quality and Convenience
- Best Practices for Storage and Application
- The Future of Lubrication: Sustainability and Innovation
The Unseen Giant: Understanding the 55 Gallon Drum of Lube
When we talk about a "55 gallon drum of lube," we're generally referring to industrial lubricants – the lifeblood of manufacturing plants, heavy machinery, automotive industries, and countless other sectors where moving parts interact. Unlike the smaller containers you might find for household or personal use, the sheer volume of a 55-gallon drum signifies its purpose: continuous, high-demand application in environments where downtime is costly and efficiency is paramount. Just as a 55-inch television offers an expansive viewing experience, a 55-gallon drum provides an expansive solution to the relentless demands of industrial friction. This substantial quantity is a testament to the scale of operations that rely on consistent lubrication. From massive presses in a stamping plant to the intricate gearboxes of wind turbines, the need for a reliable, ample supply of high-quality lubricant cannot be overstated. These drums represent not just a product, but a strategic investment in operational continuity and asset protection.More Than Just Slippery: The Science Behind Industrial Lubrication
At its core, lubrication is the process of reducing friction between surfaces in relative motion. However, the science behind industrial lubricants, especially those found in a 55 gallon drum of lube, is far more complex than simply "making things slippery." These formulations are engineered with precision, much like the precise atomic weights of elements such as Calcium (Ca 40), Manganese (Mn 55), or Iron (Fe 56) are critical in material science. Each component within the lubricant plays a vital role. Industrial lubricants are typically composed of a base oil (mineral, synthetic, or bio-based) and a carefully selected package of additives. These additives impart specific properties, such as: * **Anti-wear (AW) agents:** Form a protective film on metal surfaces to prevent direct contact. * **Extreme Pressure (EP) additives:** React with metal surfaces under high load and temperature to prevent welding and scoring. * **Corrosion inhibitors:** Protect metal surfaces from rust and corrosion, a critical function given that these lubes often "protect metal from moisture and corrosive elements." * **Antioxidants:** Slow down the degradation of the oil due to oxidation, extending its service life. * **Viscosity index improvers:** Help the lubricant maintain its viscosity across a wide range of temperatures. * **Detergents and dispersants:** Keep the system clean by suspending contaminants and preventing sludge formation. The specific blend determines the lubricant's performance characteristics, making it suitable for various applications, from hydraulic systems to gearboxes, bearings, and "machine tool slides, tables, and feed mechanisms" as seen with Truegard way lube 68 oils. The meticulous formulation ensures that the lubricant not only reduces friction but also manages heat, prevents wear, and protects components, ensuring "smooth operations" and extending equipment life.Why a 55-Gallon Drum? Scale, Efficiency, and Economics
The choice of a 55-gallon drum as the standard bulk container for industrial lubricants is driven by a confluence of factors related to scale, efficiency, and economic benefits. For large-scale industrial consumers, purchasing lubricants in this volume offers significant advantages: * **Cost-Effectiveness:** Buying in bulk almost always results in a lower per-unit cost compared to smaller containers. For operations that consume hundreds or thousands of gallons annually, this translates into substantial savings on procurement. * **Reduced Handling and Waste:** Fewer drums mean less frequent ordering, fewer deliveries, and less packaging waste. This streamlines logistics, reduces labor costs associated with handling multiple smaller containers, and minimizes environmental impact. * **Consistent Supply:** A 55-gallon drum ensures a readily available supply of lubricant, reducing the risk of running out during critical production periods. This is particularly important for machinery that requires continuous lubrication or operates around the clock. Just as a robust IT infrastructure with ample memory (e.g., a graphics card running below 55 degrees Celsius, not 91 degrees) ensures smooth digital operations, a consistent supply of lubricant ensures mechanical operations run without interruption. * **Specialized Dispensing:** Industrial facilities often have dedicated lubrication rooms or systems designed to handle 55-gallon drums, complete with pumps, filtration systems, and dispensing equipment. This allows for clean, efficient, and precise application of the lubricant, minimizing spills and contamination. * **Inventory Management:** While a large volume, a 55-gallon drum is a manageable unit for inventory tracking and rotation, helping facilities maintain optimal stock levels without over-ordering or experiencing shortages. The sheer size of the drum underscores the continuous demand in industrial settings. From a manufacturing plant in Jiangsu, with its 55 city districts and vast industrial output, to a mining operation in the remote wilderness, the need for a bulk supply of lubricant is universal.The Diverse World of Industrial Lubricants: Beyond the Basics
The term "lube" is incredibly broad, encompassing everything from personal care products to highly specialized industrial fluids. When we refer to a 55 gallon drum of lube, we are typically talking about a vast array of industrial lubricants, each engineered for specific applications and operating conditions. The diversity is staggering, reflecting the complexity of modern machinery. Common types include: * **Hydraulic Oils:** Used in hydraulic systems to transmit power, lubricate components, and dissipate heat. * **Gear Oils:** Designed for gearboxes, providing high film strength and extreme pressure protection to prevent wear on gear teeth. * **Compressor Oils:** Formulated to lubricate air compressors, resisting oxidation and deposit formation under high temperatures and pressures. * **Turbine Oils:** Used in steam and gas turbines, requiring excellent oxidation stability, water separation, and anti-foaming properties. * **Way Lubes:** Specifically designed for machine tool slides, tables, and feed mechanisms, like "Truegard way lube 68 oils," which prevent stick-slip (chatter) and ensure smooth, precise movement. * **Greases:** A semi-solid lubricant, often used where oil cannot be retained, providing long-lasting lubrication and sealing properties. Each type comes with its own set of specifications, viscosities, and additive packages, ensuring optimal performance for its intended use.Specialized Formulations for Every Need
Beyond the general categories, the world of industrial lubricants includes highly specialized formulations tailored for unique challenges. These can include: * **Food-Grade Lubricants:** NSF H1 certified lubricants for incidental food contact in food processing plants. * **Biodegradable Lubricants:** Environmentally friendly options, often "99% USDA certified biobased product," for sensitive ecosystems or operations with strict environmental regulations. * **High-Temperature Lubricants:** Designed to withstand extreme heat without breaking down, crucial in applications like ovens or furnaces. * **Low-Temperature Lubricants:** Formulated to perform in freezing conditions, maintaining fluidity and protective properties. * **Specialty Lubricants with Unique Properties:** This is where we might encounter highly niche products. While a "warming sensations formula" is typically associated with personal lubricants, in an industrial context, such a phrase could hypothetically refer to a specialized lubricant designed to indicate friction points through a temperature change, or a formulation that performs optimally by generating a slight, controlled warmth to reduce viscosity in cold starts, or even just a marketing term for a lubricant that effectively reduces heat build-up. The vastness of industrial needs means that innovation is constant, leading to highly specific solutions for complex problems. The development of these specialized lubricants is a continuous process, driven by the evolving demands of industry and the relentless pursuit of greater efficiency and sustainability.Unpacking the Benefits: Performance, Protection, and Longevity
The primary purpose of any lubricant, especially a quality product from a 55 gallon drum of lube, is to enhance the performance and extend the life of machinery. The benefits derived from proper lubrication are multifaceted and directly impact a company's bottom line and operational reliability. * **Reduced Friction and Wear:** This is the most fundamental benefit. By creating a film between moving surfaces, lubricants prevent metal-to-metal contact, significantly reducing friction and the wear that leads to component degradation. This translates directly to fewer breakdowns and longer equipment life. * **Heat Management:** Friction generates heat, which can accelerate lubricant degradation and damage components. Lubricants absorb and dissipate heat, helping to maintain optimal operating temperatures within machinery. * **Corrosion Protection:** Many industrial environments expose machinery to moisture and corrosive elements. Quality lubricants contain additives that "protect metal from moisture and corrosive elements," forming a barrier against rust and other forms of corrosion. * **Contamination Control:** Lubricants can help flush away contaminants like dirt, debris, and wear particles, preventing them from causing further damage. Some even have detergent properties to keep systems clean, helping to "clean grease, grime and other marks from most surfaces." * **Energy Efficiency:** Reduced friction means less energy is wasted as heat. This translates into lower energy consumption and operational costs for businesses.Reducing Friction, Extending Life: The Core Advantages
The direct impact of a high-quality 55 gallon drum of lube on operational efficiency and longevity cannot be overstated. Consider the claims often associated with superior lubricants: "Our 55 gallon drum of lube has been proven and validated to reduce greasing intervals up to 80% and significantly reduce temperatures." This isn't just marketing speak; it represents tangible savings and improved performance. * **Extended Greasing Intervals:** Reducing the frequency of lubrication means less labor, less downtime for maintenance, and lower overall lubricant consumption. This directly boosts productivity. * **Lower Operating Temperatures:** Cooler running machinery experiences less thermal stress, leading to longer component life and reduced risk of lubricant breakdown. * **Prevention of Costly Breakdowns:** Proactive lubrication with the right product is a cornerstone of predictive maintenance, preventing catastrophic failures that can halt production, incur massive repair costs, and even pose safety risks. Just as a marriage strengthens over years from "paper" to "iron" (Fe 56) and "copper" (Cu 63.5), a machine's longevity is fortified by consistent, quality lubrication. * **Enhanced Safety:** Properly lubricated machinery operates more smoothly and predictably, reducing the risk of mechanical failures that could lead to accidents. This aligns with YMYL principles by contributing to a safer working environment. Ultimately, investing in a premium 55 gallon drum of lube is an investment in the long-term health and profitability of industrial assets. It's about saying "goodbye to friction and hello to smooth operations."Choosing the Right Lube: Navigating Specifications and Certifications
Selecting the correct lubricant from the vast array available in 55-gallon drums is a critical decision that requires careful consideration. It's not a one-size-fits-all scenario; the wrong lubricant can cause more harm than good. This process aligns with E-E-A-T principles by emphasizing expert knowledge and authoritative guidance. Key factors to consider include: * **Equipment Manufacturer's Recommendations (OEM):** Always consult the equipment manual first. OEMs specify the type, viscosity, and performance requirements for lubricants to ensure optimal operation and warranty compliance. * **Operating Conditions:** * **Temperature:** Ambient and operating temperatures dictate the required viscosity grade (e.g., ISO VG 68 for Truegard way lube). * **Load:** High loads require lubricants with strong film strength and EP additives. * **Speed:** High-speed applications may require lower viscosity oils. * **Environment:** Presence of water, dust, chemicals, or extreme temperatures will influence additive requirements (e.g., rust inhibitors, seal compatibility). * **Base Oil Type:** Mineral, synthetic, or bio-based oils each have distinct properties regarding temperature range, oxidation stability, and biodegradability. * **Additives:** Understand the specific additives required for the application (e.g., anti-wear, anti-foam, rust inhibitors). * **Certifications and Standards:** Look for industry certifications (e.g., ISO, API, NLGI for greases, USDA Biobased Product labels). A "99% USDA certified biobased product" signifies a commitment to environmental responsibility. Navigating these specifications can be complex, often requiring the expertise of lubrication engineers or trusted suppliers. For instance, understanding the nuances of a "Truegard way lube 68 oils" means knowing its specific viscosity (68 cSt at 40°C) and its suitability for machine tool slides, not just any general lubrication task. Just as precise measurements are key for a 22-inch display's diagonal length (55.88cm), precise lubricant specifications are vital for machine health.Sourcing Your Industrial Lube: Quality and Convenience
Once the right lubricant is identified, sourcing it from a reputable provider is paramount. The quality of the lubricant directly impacts the performance and longevity of your machinery, making the supplier choice a critical part of the YMYL aspect (Your Money or Your Life, relating to asset protection and operational safety). * **Reputable Suppliers:** Look for established distributors and manufacturers known for their quality control and technical support. "MSC Direct top provider of high quality products" is an example of a type of supplier that emphasizes quality and reliability. * **Product Authenticity:** Ensure you are receiving genuine products from authorized channels to avoid counterfeit or substandard lubricants that can severely damage equipment. * **Technical Support:** A good supplier offers technical assistance, helping you select the right product, troubleshoot issues, and optimize lubrication practices. * **Logistics and Delivery:** For 55 gallon drums, efficient logistics are crucial. Consider suppliers who offer reliable delivery options, including "place your order online and pick it up at your local store for free" for convenience, or direct delivery to your facility. * **Bulk Ordering Capabilities:** Ensure the supplier can consistently meet your bulk lubricant needs, especially for a 55 gallon drum of lube. The choice of supplier is as important as the choice of lubricant itself, ensuring a steady supply of high-quality products that keep your operations running smoothly.Best Practices for Storage and Application
Even the highest quality 55 gallon drum of lube will underperform if not stored and applied correctly. Proper handling and maintenance practices are essential for maximizing the lubricant's effectiveness and ensuring the safety of personnel. * **Storage:** * **Clean and Dry Environment:** Store drums indoors in a clean, dry area to prevent contamination from dust, dirt, and moisture. * **Temperature Control:** Avoid extreme temperature fluctuations. Store within recommended temperature ranges to maintain lubricant properties. * **Proper Orientation:** Store drums horizontally or at a slight angle to prevent water accumulation on the drum top, which could lead to contamination through the bung. * **Labeling and Inventory:** Clearly label drums with product type, date of receipt, and expiry date. Implement a "first-in, first-out" (FIFO) system to ensure older stock is used first. * **Application:** * **Cleanliness:** Always use clean dispensing equipment and ensure the area around the fill point is clean before adding lubricant. Contamination is a leading cause of lubricant failure. * **Correct Volume:** Apply the correct amount of lubricant. Over-lubrication can be as damaging as under-lubrication, leading to heat buildup or seal damage. * **Training:** Ensure personnel involved in lubrication are properly trained on product identification, application techniques, and safety procedures. * **Regular Monitoring:** Implement a robust lubrication program that includes regular oil analysis to monitor lubricant condition and detect potential issues early. This proactive approach, much like the "steady period" of human life between 49-55 years, ensures consistent performance and longevity for machinery. Adhering to these best practices safeguards your investment in the 55 gallon drum of lube and contributes significantly to the overall reliability and efficiency of your machinery.The Future of Lubrication: Sustainability and Innovation
The industrial lubrication sector is not static; it's constantly evolving, driven by technological advancements, environmental regulations, and the increasing demand for sustainable solutions. The future of the 55 gallon drum of lube will undoubtedly be shaped by these trends. * **Bio-based and Environmentally Friendly Lubricants:** With growing environmental consciousness, the demand for lubricants that are biodegradable and derived from renewable resources (like the "99% USDA certified biobased product") will continue to rise. These products minimize ecological impact without compromising performance. * **Smart Lubricants and IoT Integration:** The integration of sensors and IoT (Internet of Things) technology will lead to "smart" lubrication systems. These systems can monitor lubricant condition in real-time, predict maintenance needs, and even automate dispensing, further reducing waste and optimizing performance. * **Longer-Life Lubricants:** Ongoing research aims to develop lubricants with even greater oxidation stability and wear protection, extending drain intervals and reducing overall lubricant consumption. * **Specialized Additive Technologies:** Advances in nanotechnology and additive chemistry will lead to even more specialized formulations capable of addressing unique challenges in extreme operating environments. The concept of a "warming sensations formula" might evolve into highly sophisticated, responsive lubricants that react dynamically to changing conditions. * **Circular Economy Principles:** The industry will increasingly focus on recycling and re-refining used lubricants, contributing to a more circular economy and reducing reliance on virgin resources. These innovations promise to make industrial lubrication even more efficient, sustainable, and integral to the success of modern industry. Just as platforms like "Zhihu" (知乎) continuously evolve to better share knowledge and insights, the lubrication industry strives for continuous improvement and innovation.Conclusion
The 55 gallon drum of lube stands as a silent workhorse in the industrial world, a symbol of efficiency, protection, and continuous operation. Far from being a mere commodity, the contents of these drums represent sophisticated engineering and scientific precision, tailored to meet the rigorous demands of modern machinery. From reducing friction and managing heat to preventing corrosion and extending equipment life, the benefits are profound and directly impact productivity, safety, and profitability. Understanding the diverse types, the critical role of quality sourcing, and the importance of best practices in storage and application are paramount for any industry reliant on heavy machinery. As the world moves towards greater sustainability and technological integration, the evolution of industrial lubricants, particularly those found in the ubiquitous 55 gallon drum, will continue to play a pivotal role in ensuring the smooth, efficient, and responsible operation of industries worldwide. Invest wisely in your lubrication strategy, and your machinery will reward you with unparalleled longevity and performance. **What are your experiences with industrial lubricants? Share your insights or questions in the comments below, or explore our other articles on industrial maintenance best practices to keep your operations running at peak performance!**

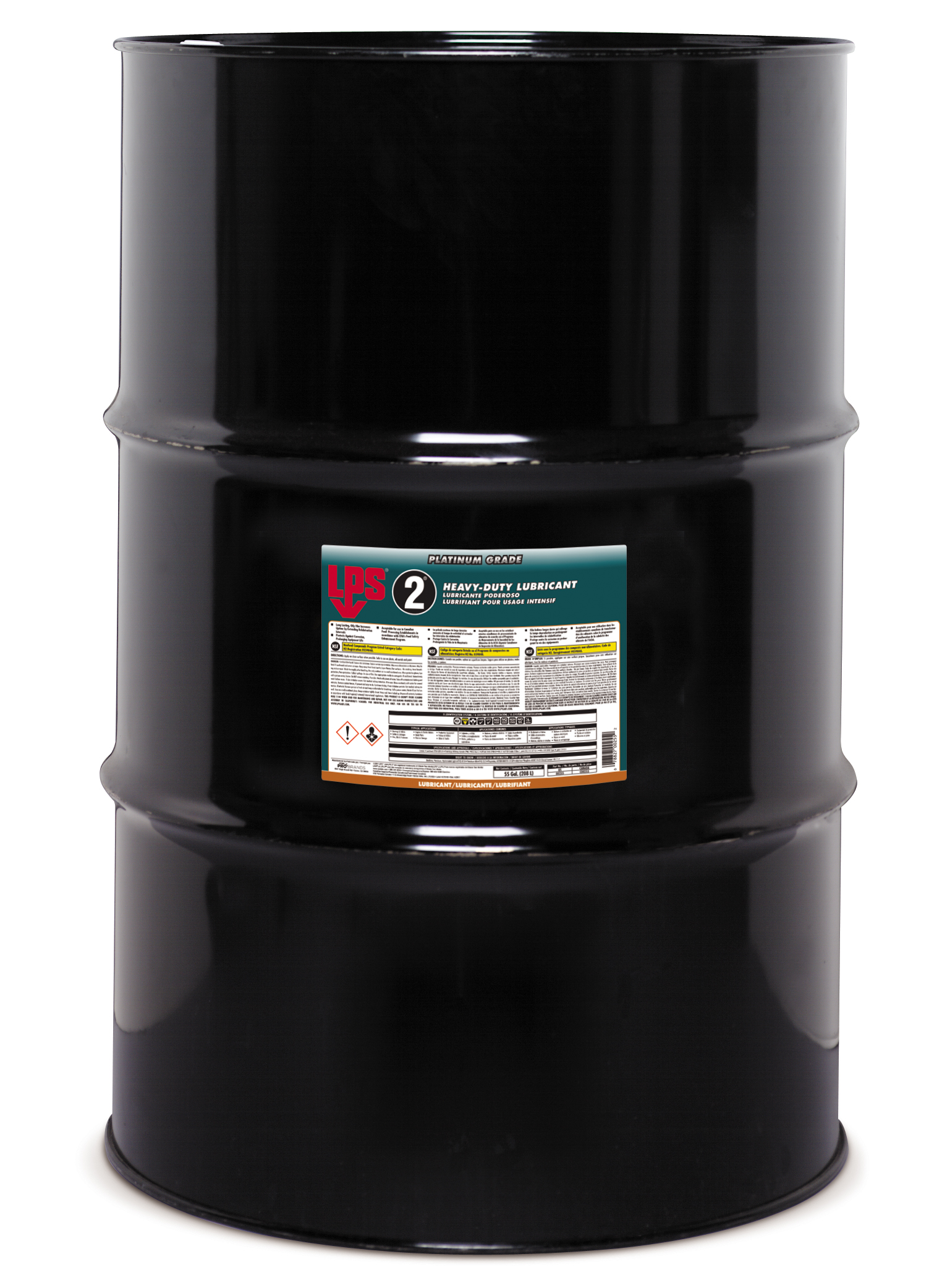