**In the dynamic world of construction, efficiency and cost-effectiveness are paramount. One area where businesses often seek to optimize expenses is equipment acquisition. This frequently leads to a significant interest in used scaffolding, offering a compelling alternative to brand-new systems. While the allure of lower upfront costs is undeniable, navigating the market for pre-owned scaffolding requires a keen eye for detail, a thorough understanding of safety protocols, and a commitment to due diligence.** The decision to invest in used scaffolding is not merely a financial one; it’s a strategic choice that impacts project timelines, worker safety, and ultimately, a company's reputation. This comprehensive guide will delve into the multifaceted aspects of purchasing and utilizing used scaffolding, equipping you with the knowledge to make informed, safe, and economically sound decisions. We will explore the benefits, potential pitfalls, essential inspection criteria, and the critical regulatory landscape that governs the use of all scaffolding, new or old.
Table of Contents
- The Appeal of Pre-Owned Scaffolding
- Understanding the Risks: Safety First
- What to Look For When Buying Used Scaffolding
- Legal and Contractual Considerations
- Maintenance and Longevity of Used Scaffolding
- The Market for Used Scaffolding: Buying & Selling
- Ensuring Compliance and Trustworthiness
- Making an Informed Decision: Your Investment in Used Scaffolding
The Appeal of Pre-Owned Scaffolding
The primary driver behind the popularity of used scaffolding is, without a doubt, its cost-effectiveness. For many construction companies, especially smaller enterprises or those undertaking projects with tight budgets, the capital expenditure for new scaffolding can be prohibitive. Pre-owned options can significantly reduce this initial outlay, freeing up funds for other critical project components or allowing for a larger inventory of equipment. This financial advantage is particularly appealing when considering the robust nature of scaffolding materials; well-maintained steel or aluminum components can have a remarkably long service life, often outlasting the projects they are initially purchased for. Beyond the immediate financial savings, there's a growing appreciation for the environmental benefits of opting for used scaffolding. In an era where sustainability is becoming increasingly important, repurposing and reusing construction materials reduces the demand for new production, thereby conserving raw materials and energy. This aligns with circular economy principles, minimizing waste and decreasing the carbon footprint associated with manufacturing and transportation of new goods. For companies aiming to enhance their green credentials and adhere to environmental, social, and governance (ESG) standards, choosing used equipment can be a tangible demonstration of their commitment to sustainable practices.Cost-Effectiveness: A Closer Look
When evaluating the cost-effectiveness of used scaffolding, it's essential to look beyond the sticker price. While the upfront cost is lower, consider the potential for repair, maintenance, and the remaining lifespan of the equipment. A comprehensive assessment should include not just the purchase price but also estimated costs for any necessary refurbishments, replacement of worn parts, and transportation. However, even with these considerations, the overall cost of ownership for quality used scaffolding often remains significantly lower than that of new equipment. This allows businesses to stretch their budgets further, investing in more extensive or higher-quality systems than they might otherwise afford, or allocating savings to other critical areas of their operation.Sustainability in Construction
The construction industry has a substantial environmental impact, from resource extraction to waste generation. Embracing used scaffolding contributes directly to mitigating this impact. By extending the life cycle of existing materials, we reduce the need for virgin resources and the energy-intensive processes involved in manufacturing new steel or aluminum. This practice also lessens the amount of construction and demolition waste that ends up in landfills. Companies that prioritize sustainability often find that incorporating used equipment into their operations not only aligns with their corporate values but can also be a positive selling point for clients who are increasingly environmentally conscious. It's a tangible way to demonstrate a commitment to responsible business practices, fostering a reputation for both economic prudence and environmental stewardship.Understanding the Risks: Safety First
While the financial and environmental benefits of used scaffolding are compelling, they must never overshadow the paramount importance of safety. Scaffolding, by its very nature, is a critical piece of equipment for working at height, and any compromise in its structural integrity can lead to catastrophic consequences, including severe injuries or fatalities. This is why the "Your Money or Your Life" (YMYL) principle applies so strongly here; the decision to save money on equipment directly impacts the safety of your workforce. There is sometimes confusion over whether to use the form "used to" or "use to" when discussing past practices, but when it comes to safety, the distinction is clear: we "used to" have less stringent safety standards, but now we "use to" implement rigorous checks. The risks associated with used scaffolding primarily stem from potential wear and tear, hidden damage, or components that no longer meet current safety standards. Unlike new equipment, which comes with manufacturer warranties and certifications guaranteeing its initial integrity, used items carry an inherent degree of uncertainty. Components might have been exposed to harsh weather, heavy loads, improper handling, or even previous accidents, leading to fatigue, corrosion, or deformation that isn't immediately apparent. Therefore, a comprehensive and expert inspection process is not just recommended; it is absolutely essential to mitigate these risks and ensure the safety of everyone working on or near the scaffolding.Rigorous Inspection Protocols
Before any used scaffolding component is put into service, it must undergo a meticulous inspection by a qualified and competent person. This individual should be trained to identify signs of damage, wear, and non-compliance with safety standards. The inspection should cover every part: frames, braces, planks, couplers, base plates, and wheels. Look for rust, bends, cracks, excessive dents, missing components, or any signs of previous repairs that might compromise structural integrity. It's not enough to simply glance at the equipment; a detailed, hands-on examination is required. For instance, while a component might look fine from a distance, upon closer inspection, it might reveal hairline cracks or stress fractures that could lead to failure under load. This level of scrutiny ensures that what you're putting your trust in is truly fit for purpose.Certification and Industry Standards
Adherence to industry standards and regulations is non-negotiable. In many regions, bodies like the Occupational Safety and Health Administration (OSHA) in the U.S. or similar regulatory authorities globally, set strict guidelines for scaffolding design, erection, use, and inspection. When acquiring used scaffolding, it is crucial to verify that the components meet current standards. Older scaffolding systems, while still functional, might not comply with the latest safety advancements or material specifications. Ensure that any scaffolding you purchase, whether new or used, comes with verifiable certifications and can be assembled in accordance with recognized industry best practices. This often means checking for markings, material specifications, and compatibility with other system components. Reputable suppliers of used scaffolding will be able to provide documentation and attest to the quality and compliance of their inventory.What to Look For When Buying Used Scaffolding
When you're in the market for used scaffolding, the adage "buyer beware" rings particularly true. This isn't just about getting a good deal; it's about ensuring the safety and longevity of your investment. A thorough visual and tactile inspection is your first line of defense. Pay close attention to the overall condition of the metal components. Are there signs of excessive rust or corrosion, especially at joints or welds? Even minor corrosion can compromise structural integrity over time. Check for bends, kinks, or distortions in frames, ledgers, and braces. These indicate that the scaffolding may have been overloaded or subjected to impact, potentially weakening its load-bearing capacity. Beyond the structural elements, examine the connections and locking mechanisms. Do pins fit snugly? Are couplers free of deformation and rust, allowing for secure attachment? The integrity of these small but critical parts is paramount for the stability of the entire structure. Wooden planks should be free of rot, excessive splitting, or delamination. Metal planks should not be bent or have significant holes. It's also vital to confirm the compatibility of all components if you're buying from different sources or adding to an existing system. Mismatched parts can lead to instability and are often a violation of safety regulations. Finally, inquire about the equipment's history. While difficult to verify completely, a seller who can provide information on previous usage, maintenance, or storage conditions offers a higher degree of transparency and trustworthiness.Legal and Contractual Considerations
The purchase of used scaffolding, like any significant asset acquisition, involves important legal and contractual aspects that demand careful attention. This is where the clarity of language becomes critical. If, in a contract, for example, the text reads, "In other words, will the work delivered on..." it implies a clear expectation of quality and suitability. Similarly, when buying used scaffolding, the contract should explicitly state the condition of the equipment, any warranties (even if limited), and the responsibilities of both the buyer and the seller. Unlike buying a new product with standard manufacturer warranties, used equipment sales often fall under "as-is" clauses, meaning the buyer assumes all risks regarding the condition of the item. Therefore, it is highly advisable to have a clear, written agreement that outlines the specifics of the transaction. This includes a detailed inventory of components, their agreed-upon condition, the purchase price, payment terms, and delivery arrangements. Consider including clauses that allow for a pre-purchase inspection by a third-party expert, or a short acceptance period after delivery during which any significant discrepancies can be reported. Understanding your legal recourse in case of a dispute is crucial. While "used for" is restricted to instruments or tools, and "used to" can be used with both senses (e.g., "this scaffolding is used for support" vs. "this company used to buy only new scaffolding"), in a contract, precision leaves no room for ambiguity. Consulting with legal counsel specializing in commercial transactions can provide an invaluable layer of protection, ensuring that your interests are safeguarded and that you are fully aware of your obligations and rights.Maintenance and Longevity of Used Scaffolding
The lifespan of used scaffolding is not predetermined solely by its age at purchase; it is significantly influenced by ongoing maintenance and proper storage. Just as one becomes "used to" a routine like drinking green tea every morning, developing a consistent maintenance schedule for your scaffolding is crucial for its longevity and safety. Scaffolding components are robust, but they are also subject to wear and tear from constant use, exposure to the elements, and handling during erection and dismantling. Regular cleaning, inspection, and timely repairs are paramount. This means removing dirt, concrete splatter, paint, and other debris that can accelerate corrosion or obscure damage. Lubricating moving parts, like pins and couplers, ensures smooth operation and prevents seizing. Furthermore, proper storage is a key factor in extending the life of used scaffolding. Components should be stored in a dry, well-ventilated area, ideally off the ground, to prevent rust and degradation. Organizing components neatly not only protects them from damage but also makes inventory management and future assembly more efficient. Any damaged or excessively worn parts should be immediately tagged, removed from service, and either repaired by a qualified professional or replaced. Attempting to repair structural components without proper expertise and equipment can be extremely dangerous. By adhering to a rigorous maintenance regimen, you can ensure that your used scaffolding continues to perform reliably and safely for many years, maximizing your initial investment and reducing the need for premature replacements.The Market for Used Scaffolding: Buying & Selling
The market for used scaffolding is robust and diverse, driven by the cyclical nature of construction projects and the constant need for cost-effective solutions. Buyers can source used scaffolding from various channels, including specialized used equipment dealers, online marketplaces, auction houses, or directly from other construction companies looking to offload surplus inventory. Each channel has its own advantages and disadvantages. Specialized dealers often offer inspected and sometimes refurbished equipment, providing a higher degree of reliability, though usually at a higher price point. Online marketplaces and direct sales might offer lower prices but require more diligence from the buyer in terms of inspection and verification. For sellers, understanding the market value of their used scaffolding is crucial. Factors influencing price include the type of scaffolding (e.g., frame, system, or tube and clamp), its material (steel, aluminum), its overall condition, age, and compliance with current standards. Well-maintained equipment from reputable brands will command a better price. It's important to accurately represent the condition of the scaffolding to potential buyers to build trust and avoid disputes. Providing clear photographs, detailed component lists, and any available maintenance records can significantly enhance a seller's credibility. The efficiency of the transaction often hinges on clear communication and transparent dealings, ensuring that both parties achieve a fair outcome in the exchange of valuable construction assets.Ensuring Compliance and Trustworthiness
For any business operating in the construction sector, ensuring compliance with safety regulations and fostering trustworthiness are not optional extras; they are fundamental pillars of operation, especially when dealing with used scaffolding. The "Expertise, Authoritativeness, Trustworthiness" (E-E-A-T) principles are directly applicable here. Expertise comes from having knowledgeable personnel who can correctly inspect and manage scaffolding. Authoritativeness is demonstrated by adhering strictly to industry standards and regulations set by bodies like OSHA or ANSI. Trustworthiness is built through transparent practices, rigorous safety protocols, and a commitment to worker well-being. When purchasing used scaffolding, the trustworthiness of the supplier is as critical as the condition of the equipment itself. A reputable dealer will be transparent about the history of the scaffolding, its previous usage, and any repairs or refurbishments it has undergone. They should also be able to provide documentation, such as proof of purchase, inspection reports, or material certifications, if available. Beware of deals that seem "too good to be true," as they often hide underlying issues that could compromise safety or lead to costly repairs down the line. It's far better to pay a slightly higher price for equipment from a trusted source that provides peace of mind and reduces the risk of accidents or regulatory fines. Investing in quality used scaffolding from a reliable vendor is an investment in your company's safety record and reputation.Making an Informed Decision: Your Investment in Used Scaffolding
The decision to acquire used scaffolding is a significant one, balancing the clear financial advantages with the critical imperative of safety. It's an investment that, when made wisely, can yield substantial returns, both in terms of cost savings and environmental responsibility. However, a hasty or ill-informed choice can lead to severe consequences, including accidents, legal liabilities, and damage to your company's reputation. This is why a comprehensive approach, prioritizing due diligence and expert assessment, is absolutely essential. Before finalizing any purchase, ensure that you have thoroughly inspected the equipment, ideally with the assistance of a qualified professional. Verify its compliance with all relevant safety standards and regulations. Understand the terms of the sale, paying close attention to contractual details and any warranties provided. Remember, while the concept of something being "used as the symbol of Paris and of France for over a century" evokes a sense of enduring quality, this doesn't automatically apply to all used equipment. Each piece of scaffolding must earn its place on your job site through rigorous verification. By adopting a meticulous and informed approach, you can confidently leverage the benefits of used scaffolding, ensuring the safety of your workforce and the success of your projects.
We hope this comprehensive guide has illuminated the path to making smart choices when considering used scaffolding. Do you have experiences with buying or selling used scaffolding that you'd like to share? Perhaps you have specific questions about inspection or maintenance? Leave a comment below to join the conversation, or share this article with your colleagues to help foster safer and more sustainable practices in the construction industry!
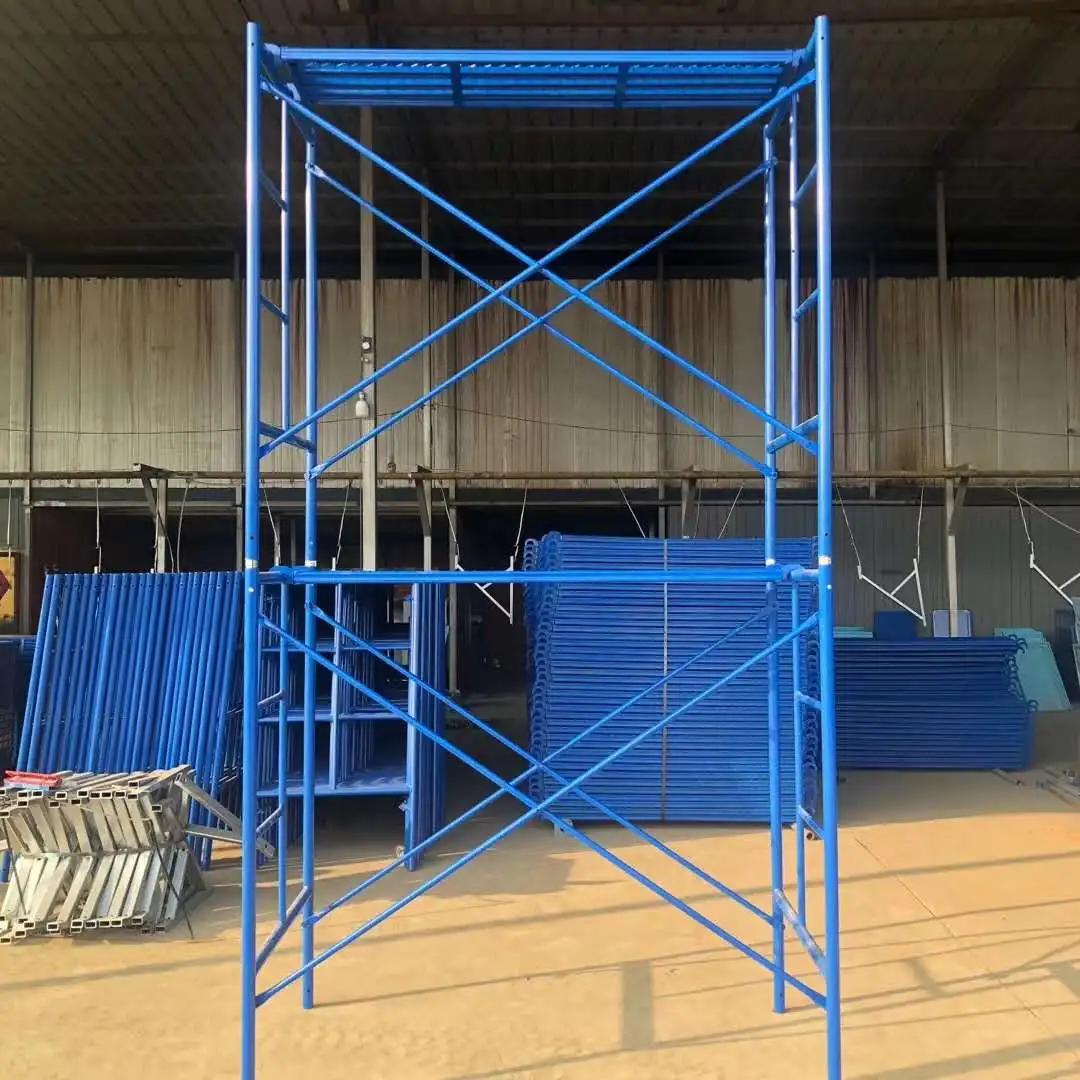

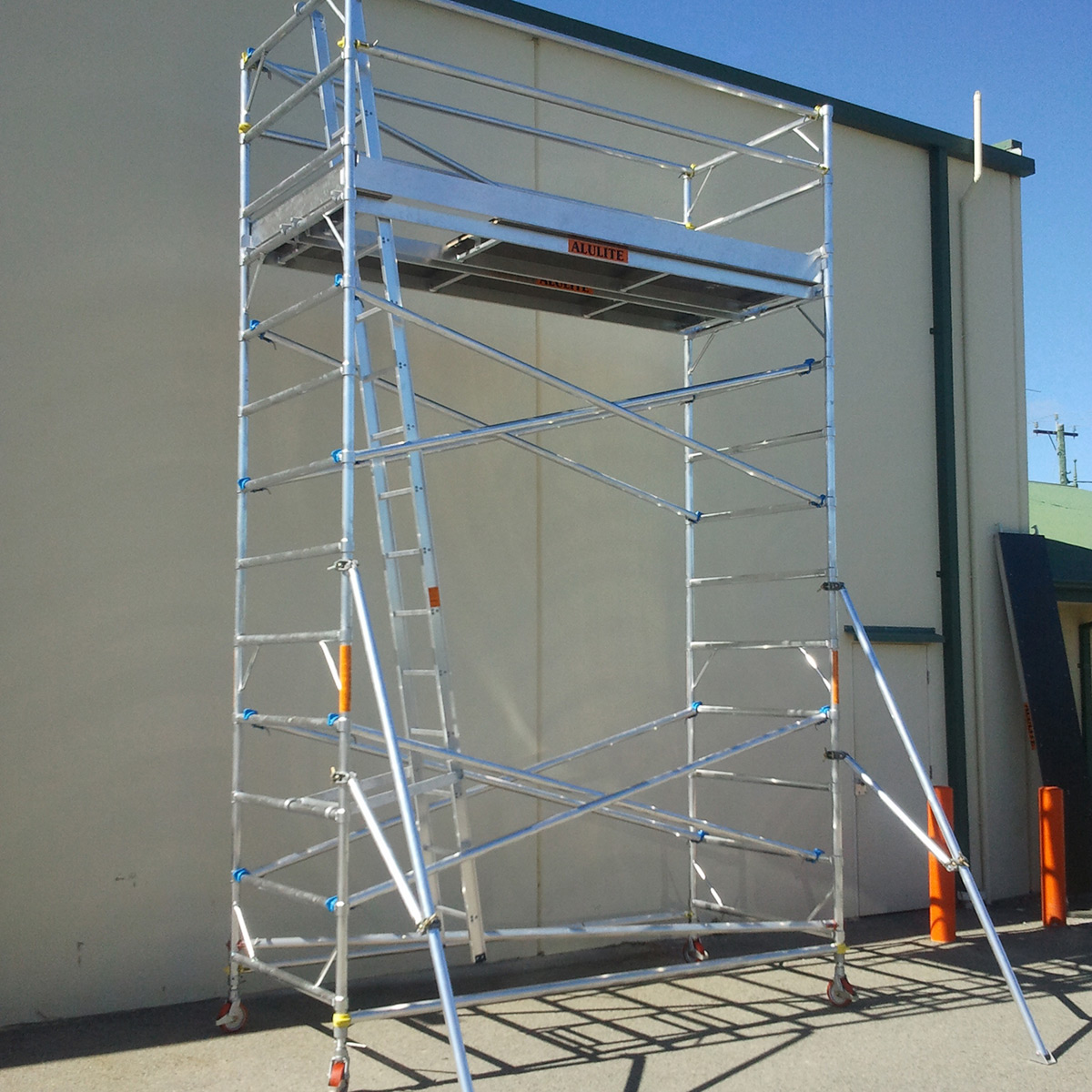